Wind turbine blade casting at the microscale

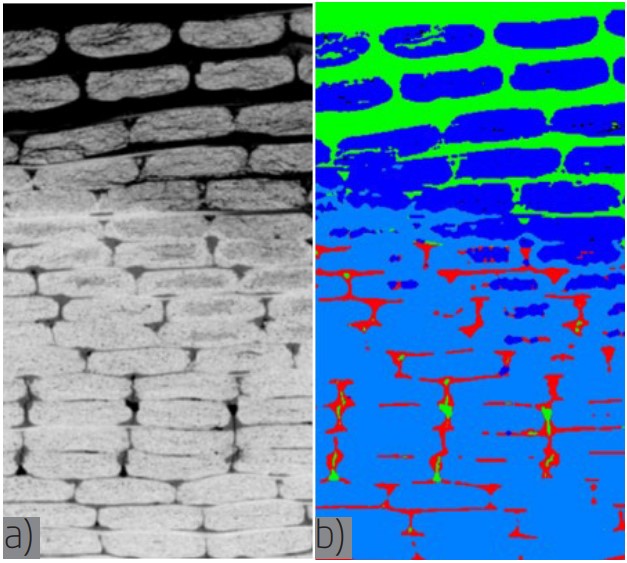
Challenge
LM Wind Power holds world records for producing the longest blades, now with lengths above 100 meters. Wind turbine blades are far too large samples to be analysed in a conventional micro-CT scanner. Therefore, the blades have to be cut in smaller pieces to be scanned, which can only be done once the resin has hardened. This means that the dynamic casting process cannot be analysed. For this reason, model samples, which imitate what happens during the dynamic process, were to be analysed.
Collaboration
LM Wind Power performed casting experiments on smaller pieces of glass fibres which were studied at the 3D Imaging Centre at DTU. This collaboration was part of the LINX project in which researchers at leading Danish universities collaborate with scientists in industry to solve industry relevant problems using advanced neutron and X-ray techniques.
Results
LM Wind Power made blade model samples for which the casting process had been abruptly stopped. By this approach, the process of resin diffusion into the fibre bundle network can be imitated. These model samples were studied by X-ray CT in regions where the resin had only partly diffused into the fibre bundle network. The analysis of the resin flow front gave insight into the resin diffusion process in and around fibre bundles. It revealed that the resin was flowing faster around fibre bundles than into the interior of the bundles. From the obtained 3D images the volume of filled fibre bundles, non-filled fibres bundles, air voids and pure resin was quantified in 3D. Complementary to fibre bundle analysis was a high-resolution scan where the resin could be observed around individual fibres in the bundles.
Perspectives
A next step would be to develop an in situ method for casting small model blades simultaneously to micro-CT measurements. With such a method the dynamics of the casting process can be better understood as this is step further to studying the realistic blade production.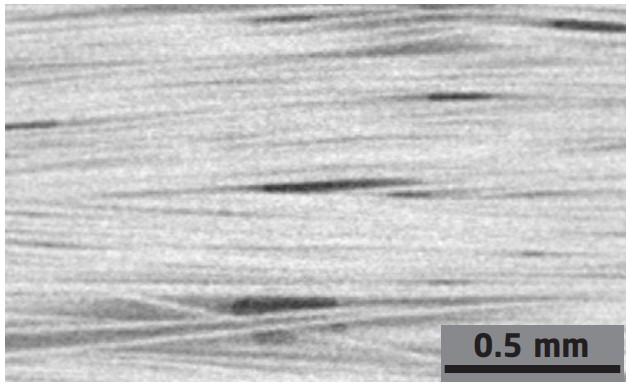