Quality Assurance of metal powders used for 3D printing

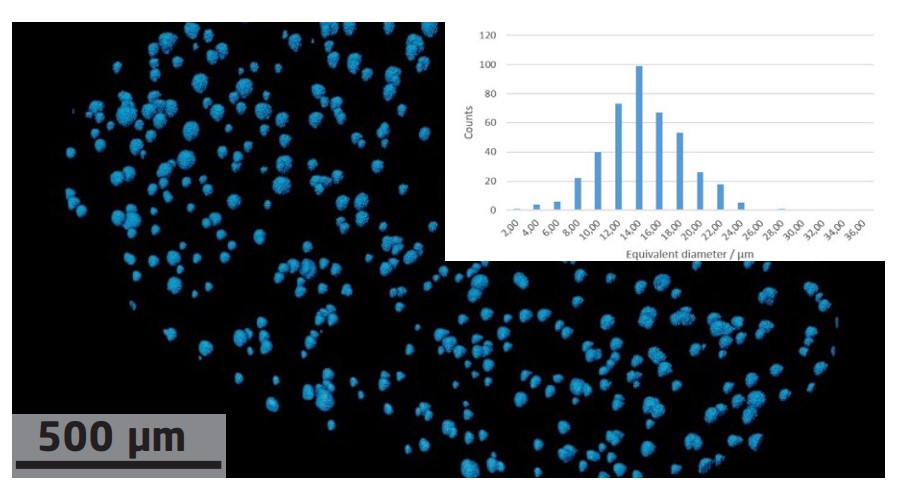
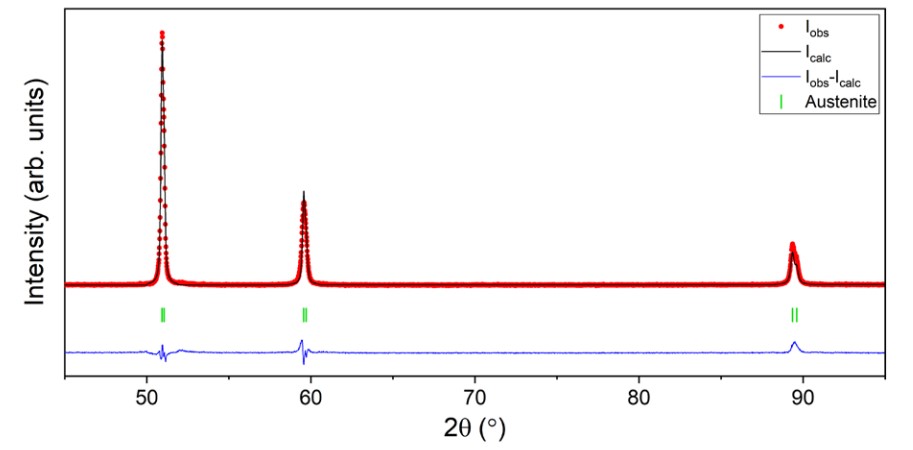
General Characterization
At FORCE Technology a variety of different characterization methods for powders were reviewed. In addition to a literature review about standards to be followed in powder-based additive manufacturing, printed samples were analysed with respect to their mechanical properties and their microstructure . Furthermore, light optical microscopy and Scanning Electron Microscopy (SEM) were performed on the powders to obtain particle size distributions. For example, for a 316L stainless steel powder, a mean particle diameter of around 20 µm with a size ranging from 1 µm to 60 µm was found using SEM.
X-ray Computed Tomography
Although SEM provides a high spatial resolution, it offers only limited access to volumetric 3D information. In contrast, X-ray Computed Tomography (CT) provides access to the full 3D structure of the sample, but at limited spatial resolution. At the 3D Imaging Center at DTU, X-ray micro CT was performed using in-house machines. For the 316L stainless steel material, a mean particle diameter of 14 µm and a size ranging from ca. 4 µm to 36 µm was obtained for a measurement performed with 3 µm spatial resolution. Also, the X-ray CT measurements showed mostly spherical particles and supplemented therefore the more precise, but only 2D, SEM measurements.
X-ray Diffraction
At Aarhus University, the crystalline phase composition of the virgin and re-used powders, as well as of 3D-printed and conventionally cast test samples, was studied using X-ray diffraction. The diffraction data were collected on an in-house diffractometer equipped with a Co Kα source. The diffraction pattern of the 316L stainless steel powder revealed for example only one crystalline phase (austenite). The same was found for the re-used powder and for the 3D-printed sample. However, the conventionally cast test sample was found to contain a minor martensite phase aside from the major austenite phase. These findings underline the complementarity of the presented methods for material characterization as they support with information about the phase composition of the materials