Analysis of folded packaging materials



Challenge
Packages for liquid food products are made of a laminar material consisting of paperboard, aluminium foil and polymers. For generating high-precision virtual models of these packages, the challenge is to describe the material’s geometry with precision as it is bent at different angles. For this purpose, the real packaging material was to be studied non-destructively in 3D. Besides studying different processing parameters and four folding angles, we also investigated the two directions in which the material can be folded. From these studies, we could extract virtual 3D representations which will be the basis for further modelling at Tetra Pak. In addition to obtaining geometric input for modelling, Tetra Pak is also interested in quantitatively measuring how the layers behave when being folded.
Collaboration
Through the collaboration between Tetra Pak and the 3D Imaging Centre at DTU, the packaging material was characterised using micro X-ray computed tomography (CT) and in-house developed analysis tools. This collaboration was part of the LINX project, in which researchers at leading Danish universities collaborate with scientists in industry to solve industry relevant problems using advanced neutron and X-ray techniques.
Results
The packaging material was scanned using a Zeiss Xradia 410 X-ray CT setup. Based on the obtained 3D images, the aluminium layer and the opposite clay coat layer needed to be extracted virtually. To do this, we applied a geometric transformation and a subsequent surface detection method at each folding angle. Subsequently, the paperboard texture was used to align the layers at the different folding angles. After alignment, the layers are a precise representation of the geometry that Tetra Pak can use as an input to modelling and simulation. To quantify how the material behaves during folding, the distance between the inner and outer layers was used, which lead to discover that the behaviour is different depending on the direction of the fold. For now, this tool was applied to one specific material. In the future, it could be used to study the effect of further processing parameters or other layer compositions. In addition, faster X-ray CT acquisition would allow to study the folding process in situ, that is during folding.
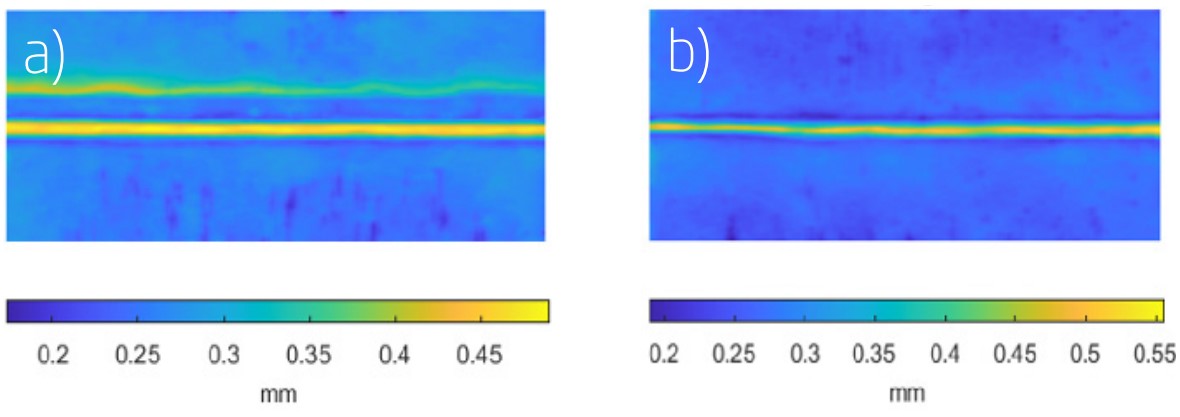