Studying the pore structure of a catalyst
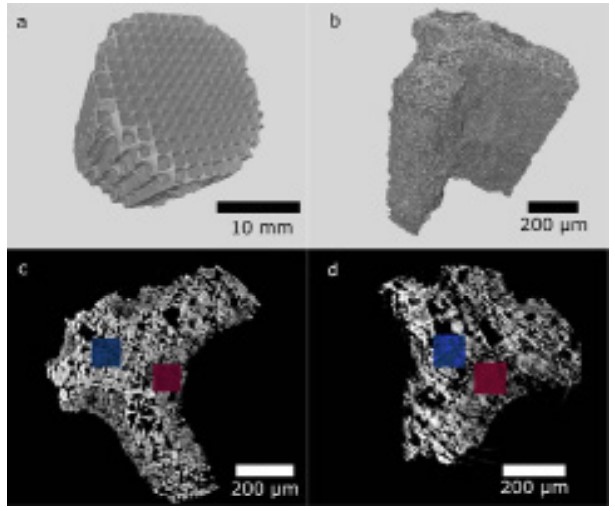

Project
The work is part of a research collaboration with the group of prof. Dr. Jan-Dierk Grunwaldt at the Institute for Chemical Technology and Polymer Chemistry at the Karlsruhe Institute of Technolgy. As research at the 3D Imaging Centre at DTU focuses on the development and application of X-ray Computed Tomography (CT), CT was applied in this project to study the microstructure of a catalyst material. The project was part of the general development activities within the LINX project, in which researchers at leading Danish universities collaborate with scientists in industry to solve industry relevant problems using advanced neutron and X-ray techniques.
Challenge
In order to study the porosity of a catalyst spatially resolved in 3D, different microscopy techniques need to be combined to span length scales ranging from micropores (>2 nm), via mesopores (2-20 nm) to macropores (>20 nm). While electron tomography and pthychographic X-ray computed tomography were used to cover the nanometre to micrometre scale, X-ray CT covering the micrometre to centimetre scale, was performed at the 3D Imaging Centre at DTU to study the full structure of three catalysts (fresh and differently aged).
Results
At the 3D Imaging Centre at DTU, the three catalyst samples were investigated at different zoom levels, revealing the full catalyst structure with approx. 80 µm, some channels with approx. 15 µm and a single channel with approx. 2 µm spatial resolution. A relatively uniform washcoat distribution was found, which is needed for proper application of the catalyst. In addition showing the evolution of cracks after ageing, the high-resolution scans on one channel reveal differences in the pore size distribution for a fresh and severely aged catalyst, indicating that the pore sizes increase during ageing. These results match with the findings obtained with the other techniques. Though each method has its own benefits and challenges, such complementary approaches are needed to study complex systems. Further information: DOI: 10.1021/acs.jpcc.9b06541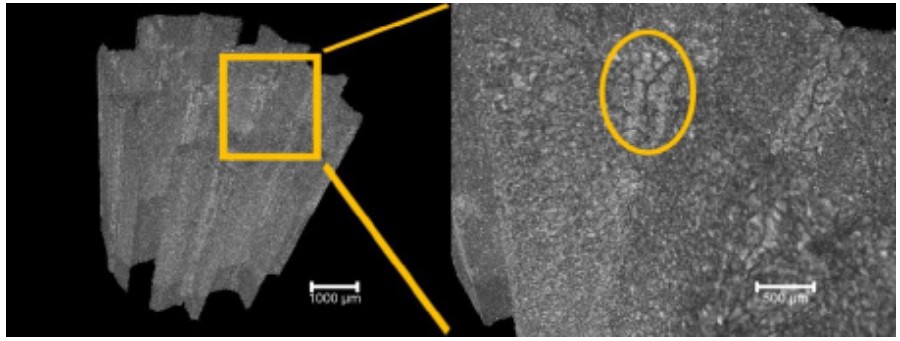