Optimizing multiscale materials in wind turbine blades
Challenge
A wind turbine blade consists of a strong load-carrying laminate and lighter sandwich panels made of glass fiber composites and balsa wood. The multiscale nature of the sandwich panel is difficult to investigate with classical microscopy methods, since it requires dynamic measurements, which would show how glass fiber composites, balsa wood and resin interact and evolve in time.
Collaboration
LM Wind Power entered a collaboration with the Imaging Industry Portal in order to explore the possibilities X-ray could offer compared to other imaging techniques. The company sent cm-scale samples of blades, which were scanned on a µ-CT scanner in Lyngby.
Results
The 3D images delivered to LM Wind Power had an unexpected high level of detail and gave the company’s engineers a unique insight in the pore microstructure of balsa wood, which is a key issue to understand the role of this material in the blade’s robustness
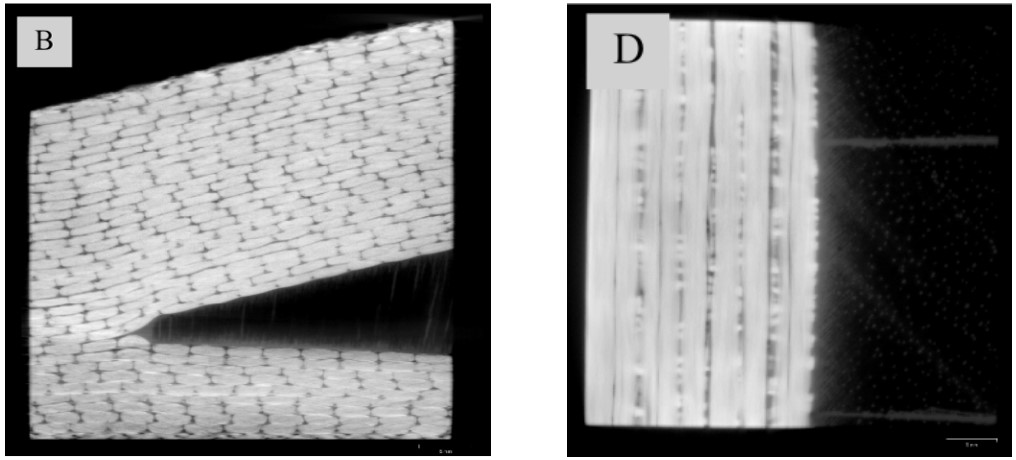
“We can now gain a much better understanding of how our materials work together and how damages might occur. This will definitely help us design and construct even more efficient and reliable blades.”